Learn more about the EFAFLEX insulating deep-freezer-door SST-TK 100
The design of the freezer high speed door system was a real challenge. In fact, there were two challenges, physics, and logistics!
In deep freezer areas, the physical laws, or to be more specific, thermodynamics, challenged us in three different ways:
- We need to compensate for temperature differences
- We need to avoid icing
- And finally, we needed to minimise energy loss
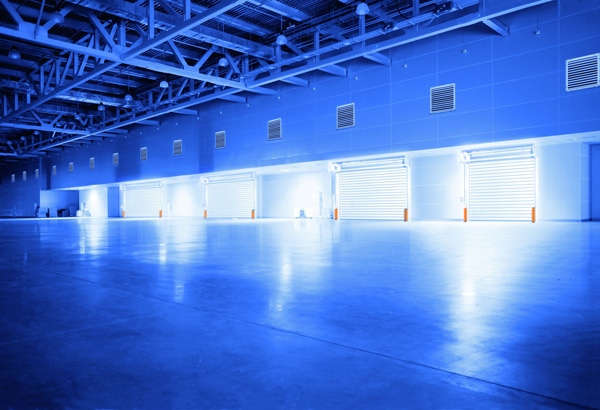
What are the requirements for insulating warehouse
door systems in deep freezer environments?
The logistic challenges are specified through three different aspects:
- Safety for people and equipment have top priority
- We need to guarantee the logistic flow
- And finally, warehouse door automation plays a critical role
Let’s have a look at the physics details:
Cold Environment
We have to deal with temperature differences of around 35 to 40 degrees Celsius in deep freezer areas. These temperature differences result from the operator's requirements for efficiency with insulated warehouse doors. We can usually find three different temperature areas: 1. The deep freezer storage itself at minus 30 °C 2. The preparation area with approximately 4 - 8°C 3. Any adjacent warehouse ambient areas These temperature differences, in connection with humidity, lead to icing. This can result in functional limitations of the insulating warehouse doors.
What leads to this icing effect?
Physical conditions like humidity, with the introduction of ambient air and temperature, will automatically cause specific reactions. The warmer air is, the more humidity it can contain. This humidity will condense at colder surfaces when the surface temperature is low enough, which leads to icing. The relative humidity, shown in a certain percentage, says nothing about the amount of water in the air.
The challenges of warehouse air streaming in and out.
What happens during the opening of the warehouse industrial door?
We find two contrary air movements during the door’s opening, which will balance the temperatures. Cold air will stream out of the freezer area in the lower half of the door, while warm air streams into the deep freezer area in the upper half of the door opening. At the lower half of the door, the outflow of cold air results in a cooling down of the warehouse door’s surface. When the warm air cools down, it loses its moisture through condensation on the contact surfaces. When these cold surfaces meet the warm air, moisture, condensation, and icing will start. The same will happen in warehouse areas, where a door doesn’t seal perfectly, or permanent cold air flow penetrates from the freezer. This icing can result in heavily ice-packed equipment, damage the function, and compromise safety.
As industrial high speed door engineers and designers, this is what we have learned:
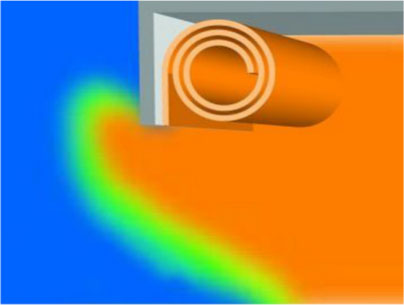
Effective insulating door seals
The more effectively the freezer warehouse door is sealed, the lower the air leakage of the system.
Condensation reduction
Reducing condensation and, therefore, the icing.
The importance of air-tight environments
It is essential for a industrial door in a deep freezer application to be as air tight as possible.
Energy efficiency
Temperature differences will automatically result in energy loss, which needs to be minimised to be energy efficient. Therefore, effective sealing and insulation measures have to be taken.
We have developed a highly insulated high-speed door, combined with an extremely effective sealing solution. The EFA SST-TK 100
Let’s look at the sample of the warehouse door panel and how this was realised.
The insulated panels of the TK 100 are completely thermally separated and are 100 mm thick, optimising insulation properties. The U-value of the complete door is as low as 0,62 W/m²K.
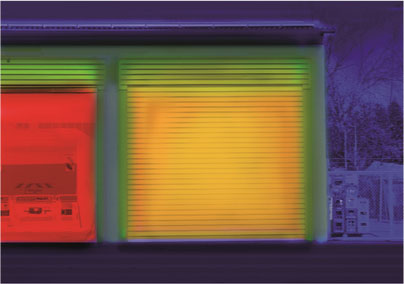
This thermal image of a conventional roller door clearly shows the loss of heat to the outside.
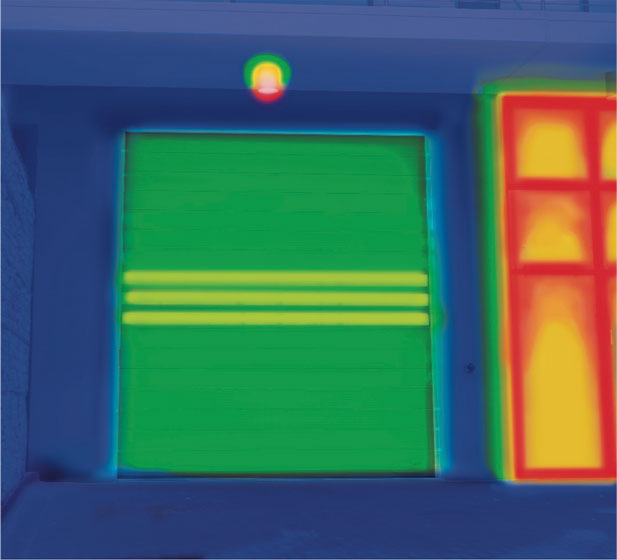
The thermally insulated EFA-THERM laths of the EFA-SST considerably improve the thermal insulation, thus lowering your energy costs.
Here we see the middle seal. You find a seal between all neighbouring door panels, preventing uncontrolled air exchange. These seals are equipped with highly energy efficient heating, using an effective 48 V, safe, low voltage system. The heating cables used just 20 Watt per metre length (approx). To get a rough idea: A complete door of 2,5 x 3 m in size has a total heating capacity of approx. 650 Watts.
Learn more about the AFM Active Track Mechanism
The unique detail of this industrial door is the sealing towards the wall. EFAFLEX designed a mechanism that enables the complete door-blade to move horizontally, forming an extremely effective perimeter seal. At floor level, the door is sealed using a heated safety-edge profile. This system guarantees that all four sides of the door are equipped with heated seals. The rubber material is specially selected. It stays flexible and does not harden when cold. Only a genuinely flexible material can optimise the seal. Cold rubber gets stiff and rigid, and if it isn’t flexible, it won’t seal the opening. To protect the perimeter seal from wear and to extend its lifetime, The complete door-blade moves horizontally just after leaving the “closed “position for about an inch. Because of this horizontal movement, the door can seal the deep freezer almost hermetically. All joints and edges around the SST-TK 100 door are sealed and heated. The air permeability of this door was tested and confirmed to reach class 4, according to DIN EN 13241-1.
After having a close look at the physical aspects, we now concentrate on the logistics.
Easy flow of logistics
Despite this extensive technology, the TK 100 door opens at speeds up to 1,5m/s and closes at speeds up to 0.5 m/s. The TK 100 door was designed as an industrial door intended for intensive use – up to 200,000 operating cycles per year, with a minimum life expectancy of 10 years. A higher number of operating cycles do not cause a problem but will influence the number of maintenance visits required.
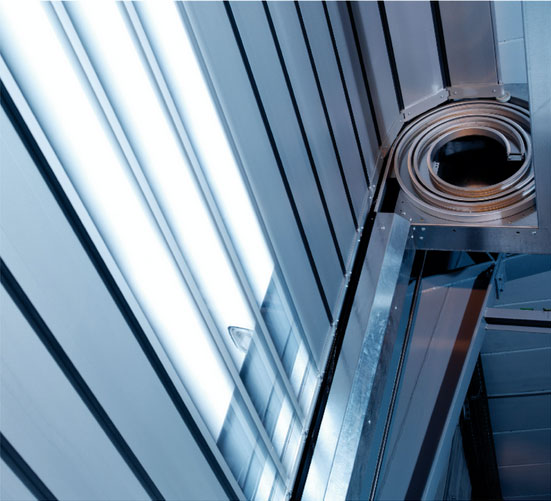
Warehouse safety
We had to think about industrial door safety, too. To protect the worker from a moving warehouse door and the door from getting damaged. The TK 100 door is equipped with a Door-Light-Grid (TLG) and a safety edge. The TLG is a touch-free safety-system, which secures the door opening up to a height of 2.5 meters above floor level. As soon as the TLG is activated, the door automatically stops briefly before returning to the fully open position. After clearing any obstructions from the door opening (the TLG protected area) the programmable timer will activate, and the door will close automatically. The insulated warehouse door is fitted with a mechanical hand release mechanism, utilising the counterbalance springs in the door. This enables manual door opening, perhaps during a power cut, to provide immediate access through the doorway.
Here we see the control of the TK 100, the most advanced door controller on the market today, the EFA-TRONIC Professional. A microprocessor control with an integrated frequency converter. Designed to be readily integrated with building management and other control systems such as a conveyor or similar. The display clearly shows the door status and the number of completed cycles. It also shows error or fault codes immediately, helping with remote diagnosis. The system is compatible with standard methods of activation and supplementary safety systems.
Using WI-FI technology, the warehouse door system can also be integrated into intelligent door networks utilising available WI-FI technology. EFA-SmartConnect enables communication directly from the door controller, providing live operating data seamlessly to a smart-phone or tablet.
This optimises service and maintenance attendance while making diagnosis more efficient and therefore, more cost effective.
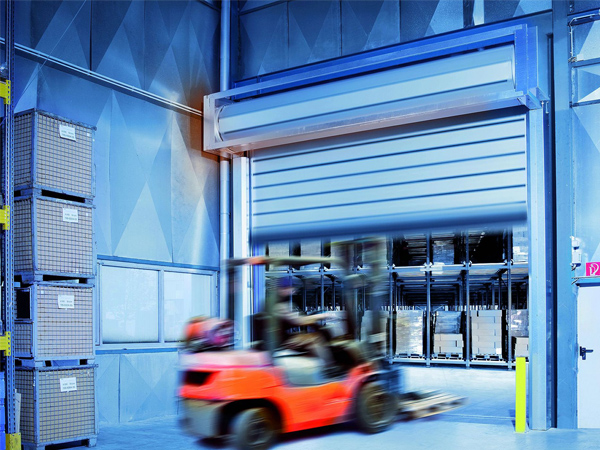
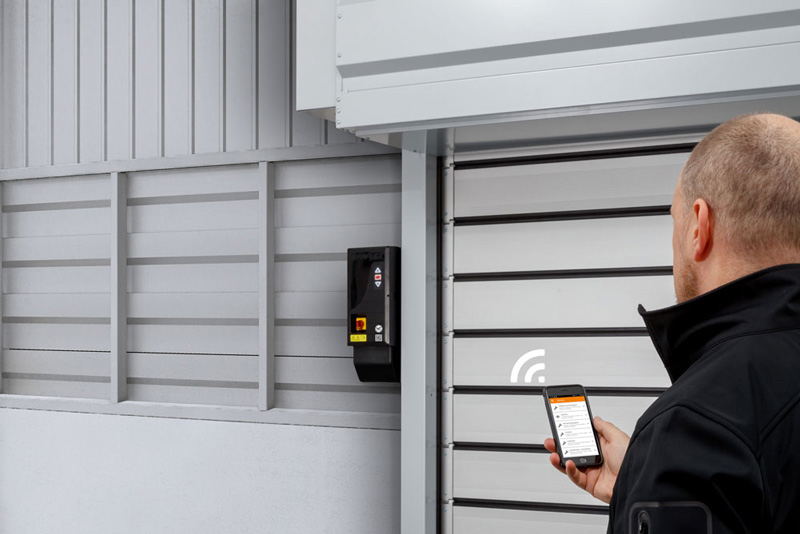